
As mentioned above, copper concentrate is most often refined using equipment at a different location than company mine sites.Ĭoncentrate producers sell a concentrate powder containing 24 to 40 percent copper to copper smelters and refiners. Mining companies may sell copper in concentrate or cathode form. This copper cathode can be sold as is, or can be made into rods or starting sheets for other electrolytic copper cells. This solution goes through the electrowinning process, which plates copper in the solution onto a cathode. Next, sulfuric acid is added to strip the copper from the organic solvent, producing an electrolytic solution. Solvent extraction begins with an organic solvent, which separates copper from impurities and unwanted material. This newer refining technology became widely adopted in the 1980s, and according to the Copper Development Association, roughly 20 percent of the world’s copper production is now produced via this process. The more common refining method is solvent extraction and electrowinning, or SX/EW. After enough copper has been plated, the copper is then further refined. The least common method is cementation, in which an acidic solution of copper is deposited onto scrap iron in an oxidation-reduction reaction. In hydrometallurgy, copper concentrate undergoes refining via one of a few processes. How is copper extracted by hydrometallurgy? Once charged, the pure copper collects on the cathode and is removed as a 99 percent pure copper product. Finally, to completely deoxidize the copper, either phosphorus is added to it to form P2O5, or the copper is cast into copper anodes and placed in an electrolytic copper cell. In fire refining, air is blown through the copper to oxidize impurities into slag then wood is added to help reduce the oxidized copper through chemical reactions, leaving refined copper behind to be processed into copper cathode.
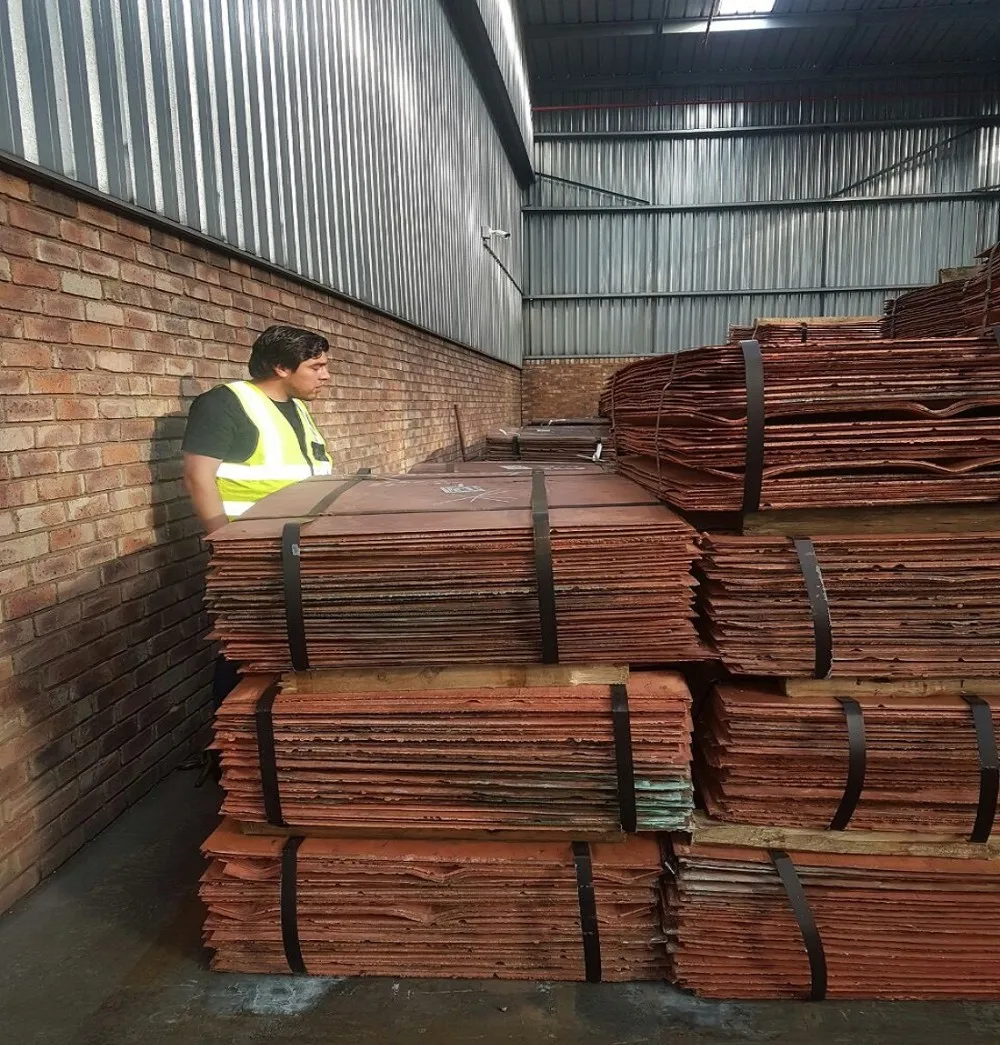
A variety of chemicals are added to the converter, and these react with the copper to form converted copper, called “blister copper.” The blister copper is recovered and is then subjected to a process called fire refining. The slag is discarded and the matte is recovered and moved to a cylindrical vessel called a converter. The matte layer, on the bottom, contains the copper, while the top slag layer contains the impurities. Chemical reactions that occur during the heating process cause the concentrate to segregate into two layers of material: a matte layer and a slag layer.

In pyrometallurgy, copper concentrate is dried before being heated in a refining furnace. How is copper extracted by pyrometallurgy?
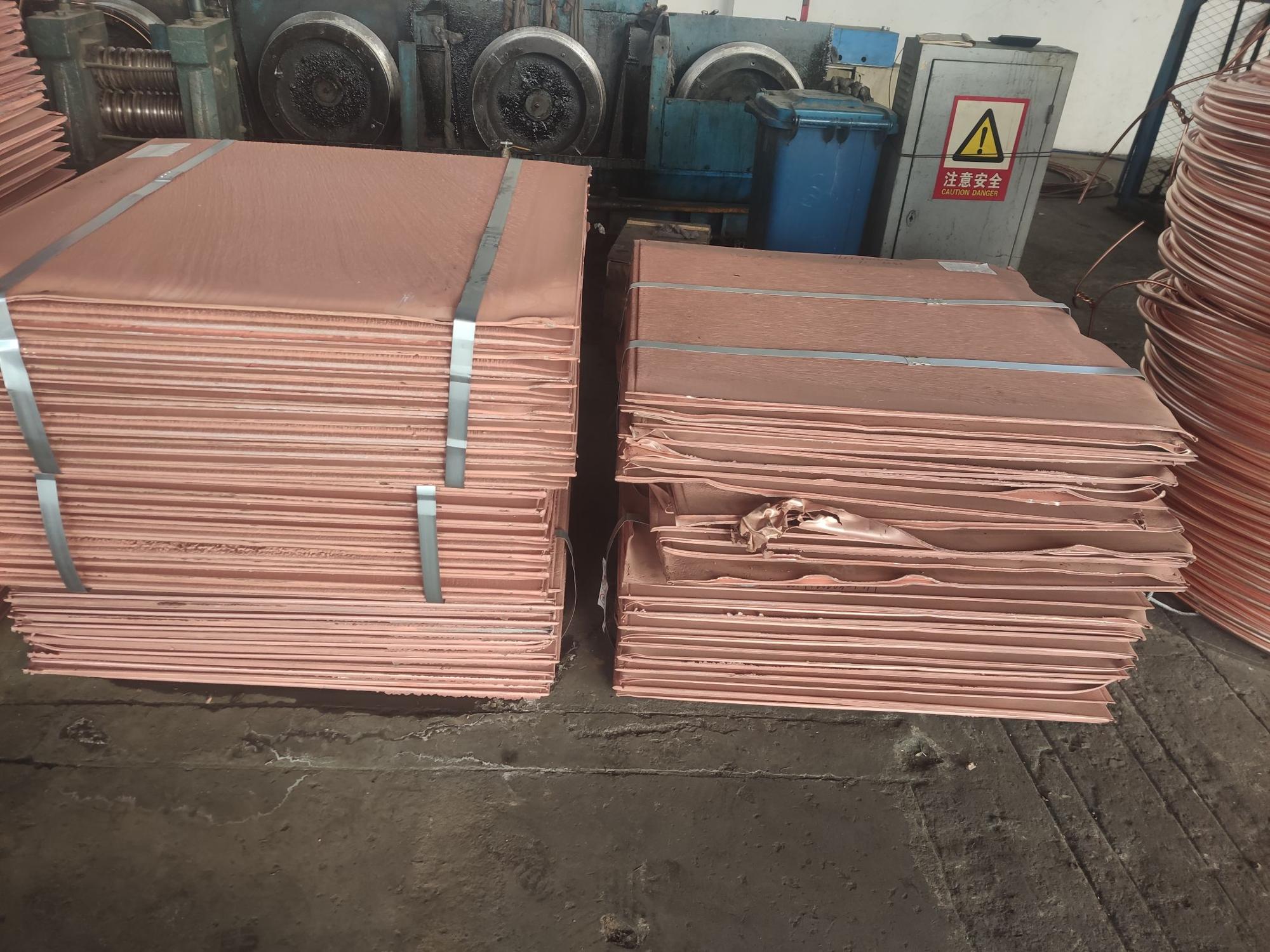
